- Products and Solutions
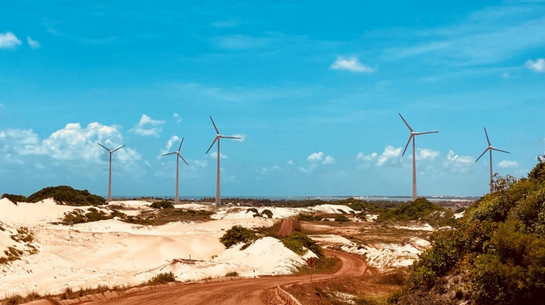
Neoenergia innovates in the inspection and maintenance of wind blades with the SmartBlade project
Neoenergia has developed an innovative project that has been changing the conventional way of managing the maintenance of one of the most important elements of wind turbines: the blades.
The new system manages the maintenance of the blades of more than 230 wind turbines of the company in Brazil. The system uses state-of-the-art digital technology, whose main tools are drones (which fly over the blade), robots (which do the internal inspections of the blades) and a software with Artificial Intelligence.
The implementation of the pilot project under development will take place by the end of 2023 and, after analyzing the results and efficiency of the tool, the company will be able to expand the project for application in all its assets in wind energy.
The project, which involved a budget of R$ 1.6 million, was developed to standardize and improve the process of inspection and management of paddle maintenance. The standard tool for this type of inspection is a digital camera, with a long-range lens and a standard checklist filled out manually by the inspector.
The new technology is more efficient than conventional practice since it inhibits human error. Also the downtime for a standard inspection is an important factor that was considered in the study. In addition to increasing reliability, the technology increases productivity as it optimizes time and streamlines the entire maintenance process.
Basically, the project consists of the application of drone and robot technology for autonomous capture of very high quality images, standardized and with a very short time – they are 10 minutes per shovel.
The drone makes the external inspection of the blades, taking thousands of photos of each one, which will later be processed by a software specially developed for compilation and identification of patterns with the help of Artificial Intelligence. The software is able to identify from the smallest damages, almost imperceptible to the naked eye, to the most serious and requiring greater attention. The same happens with the robot, which makes the images of the inside of the blades and then they are processed with the same technology.
The software is embedded in an easy-to-navigate, intuitive web platform that delivers to the user all the damages that were detected in the inspections, their degree of complexity and the technical recommendations to act on each one.
Recommendations range from maintaining routine inspections at a certain time interval to analyze the evolution of the damage, to recommending immediate repair or at a certain interval. In addition, various forms of filters are applicable on the platform in such a way that the manager can analyze the damage of his fleet in the way that best suits him. This significantly facilitates the maintenance management of this important component of wind turbines. Acting preventively in maintenance results in less energy loss.
The average time to manufacture, transport and replace a shovel is around 12 months. If the blade is no longer manufactured, this replacement time can be much longer, resulting in very impactful energy losses. In addition, the cost of a shovel is much higher than the investment cost of the project.
If we consider that the insurance will cover the material damage, only the cost of the deductible is also higher than the investment of the project. It is important to note that this level of detail and technical recommendations that the tool provides, allows the plant manager to make a repair schedule well in advance, ensuring the shortest downtime and also the resources needed for the repair.
" Neoenergia's investment in this project is extremely relevant for the operation and maintenance area. With the application of advanced technologies such as drones, robots and AI-powered software, we are optimizing the efficiency of inspection and maintenance of wind turbine blades. This innovative approach, which aims to standardize and improve the process, brings greater reliability, reduces downtime and allows for more accurate management of detected damages. We look forward to expanding the project after the completion of the pilot and reaping the benefits across our fleet of wind turbines," said Rodrigo Ferrari, Neoenergia's Renewable Operation and Maintenance Manager.
News
2025-07-01
Carbon2Nature Brasil anuncia parceria inédita com Biomas em projeto de restauração de floresta nativa no país
2025-06-25
Pedro Azagra é o novo CEO do Grupo Iberdrola
2025-06-24
São João 2025: campanha da Neoenergia alerta sobre os perigos de soltar balões em festas juninas
2025-06-17
Neoenergia é a marca mais valiosa do setor elétrico brasileiro
2025-06-16